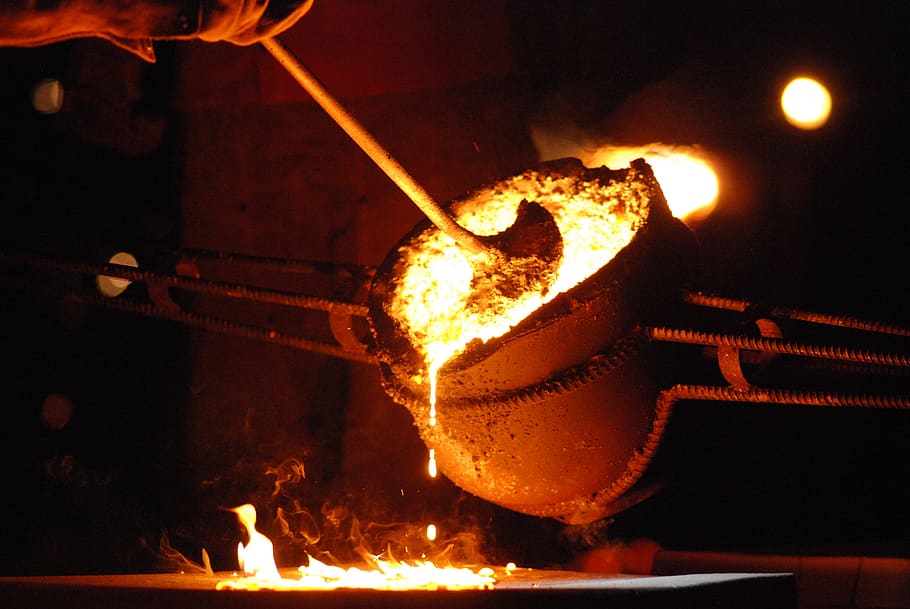
In the vast world of metal fabrication, the art of casting and finishing stands as a testament to precision and craftsmanship. From the shimmering skylines to the intricate components that power our everyday lives, casting plays a pivotal role. In this exploration, we delve into the diverse techniques, uncovering the nuances of Aluminium Die Casting, Gravity Die Casting, Low-Pressure Die Casting, Sand Casting, and the crucial finishing touch of Casting Porosity Sealing & Impregnation.
Aluminium Die Casting: Forging Strength and Versatility
The Melting Pot
In the realm of metalworking, Aluminium Die Casting emerges as a frontrunner. The process involves melting aluminium alloy and injecting it into a die under high pressure. The result? Intricately detailed components with high tensile strength, ideal for a myriad of applications, from automotive parts to electronic housings.
Rapid Production, Unmatched Precision
Aluminium Die Casting is renowned for its rapid production capabilities. The efficiency of this process lies in its ability to produce complex shapes with tight tolerances, meeting the demands of modern engineering and design.
Gravity Die Casting: Where Gravity Takes the Lead
The Controlled Descent
Gravity Die Casting operates on a fundamental principle – harnessing the force of gravity. Molten metal is poured into a permanent mould, allowing gravity to facilitate the filling process. This method is particularly advantageous for producing components with superior surface finishes and dimensional accuracy.
Cost-Effective Excellence
Gravity Die Casting strikes a balance between cost-effectiveness and high-quality output. With reduced machining requirements and minimal post-casting processing, it stands as an efficient choice for various industrial applications.
Low-Pressure Die Casting: Bridging Precision and Affordability
Pressurised Precision
Low-Pressure Die Casting marries the precision of high-pressure techniques with the cost-effectiveness of gravity casting. By applying low pressure to the molten metal, intricate details are achieved, making it suitable for components where both complexity and budget considerations come into play.
Complex Geometry, Simplified Costs
Low-Pressure Die Casting excels in the production of components with complex geometries. The method allows for intricate designs without the exorbitant costs associated with some high-pressure processes.
Sand Casting: The Time-Honoured Artistry
Shaping in the Sands of Time
Sand Casting, an ancient method refined over centuries, remains a cornerstone of metal casting. The process involves creating a mould from compacted sand and pouring molten metal into it. While traditional, Sand Casting offers versatility and is well-suited for both small and large-scale productions.
Versatility in Material Choices
One of the key advantages of Sand Casting lies in its versatility in material selection. From aluminium and brass to iron and steel, Sand Casting accommodates a wide range of metals, making it a preferred choice for diverse applications.
Casting Porosity Sealing & Impregnation: Sealing the Gaps
The Imperfection Challenge
Casting porosity, characterised by tiny voids or pores in cast metal, can compromise the integrity of components. Sealing these imperfections becomes paramount, and that’s where Porosity Sealing & Impregnation steps in.
The Sealing Solution
Porosity Sealing & Impregnation involves filling the pores with a sealant, enhancing the structural integrity of the casting. This process ensures that the final product meets stringent quality standards, particularly in applications where strength and reliability are critical.
Finishing Touch: Elevating the Craft
Beyond the Pour: Navigating the Finishing Landscape
Finishing touches are the signature of excellence in casting. Whether it’s a polished sheen or a protective coating, the final steps in the process add both aesthetic appeal and functional durability to the components.
As we journey through the realms of casting and finishing, it becomes evident that each technique contributes to the symphony of metalwork. From the swift precision of Aluminium Die Casting to the time-honoured artistry of Sand Casting, and the meticulous sealing process of Porosity Sealing & Impregnation, casting is a craft that fuses tradition with innovation. In this dance of molten metal and meticulous technique, the brilliance of casting and finishing truly comes to life.