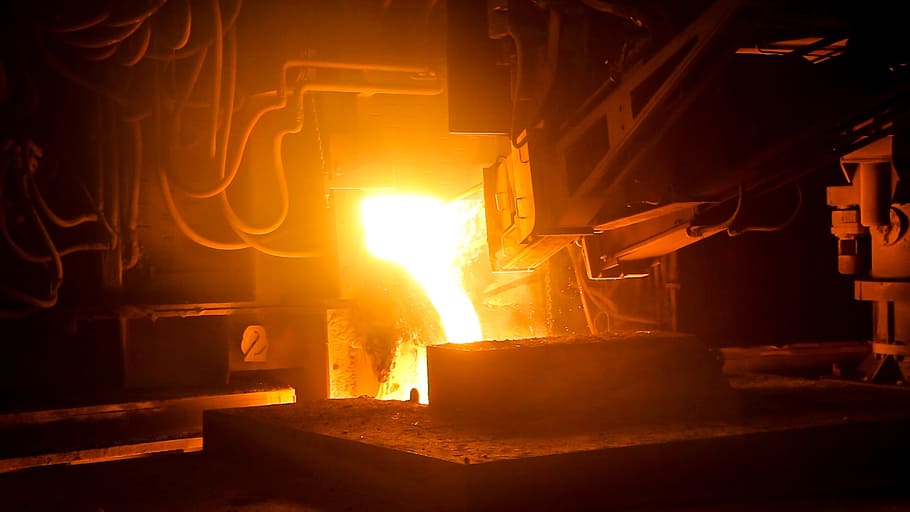
Whether it’s a small part for a precision instrument or a large component for heavy machinery, metal casting plays a critical role in shaping the products we rely on every day. From gravity die casting to sand casting, the right approach ensures that each piece meets exacting standards of strength, durability, and performance. A professional casting company provides tailored solutions, backed by expertise and technology, to meet the needs of various industries.
Why Die Casting is Essential for Modern Manufacturing
Aluminium die casting is one of the most popular methods for creating components with a high strength-to-weight ratio. Aluminium is priced for its lightweight and corrosion-resistant properties, making it ideal for automotive, aerospace, and electronics applications. Die casting allows for intricate designs and smooth finishes, giving manufacturers flexibility and precision without sacrificing quality.
This method also enhances sustainability. Aluminium is recyclable, meaning that leftover material from the die-casting process can be reused, reducing waste and promoting Eco-friendly manufacturing practices. It’s a win-win for businesses and the planet.
Gravity Die Casting: Where Strength Meets Simplicity
For manufacturers looking for a balance between efficiency and robustness, gravity die casting is a go-to choice. Using gravity rather than external pressure, this process creates parts with exceptional mechanical properties. Gravity die casting works best for medium to high-volume production runs and is a versatile option for industries requiring durable yet cost-effective solutions.
Its applications are diverse, from household fixtures like faucets to intricate components in industrial machinery. The simplicity of this method keeps costs manageable, while the quality remains uncompromised.
Low-Pressure Die Casting: Precision at Its Finest
When precision is non-negotiable, low-pressure die casting delivers. This method utilises controlled pressure to fill moulds, resulting in parts with excellent dimensional accuracy and minimal porosity. Low-pressure die casting is especially suited for automotive parts like wheels and structural components, where even minor flaws can compromise safety and performance.
Manufacturers benefit from the consistency and repeatability of this process, ensuring that each part meets exact specifications. Whether it’s a prototype or a full-scale production run, low-pressure die casting offers unmatched reliability.
Sand Casting: Timeless Versatility
For projects requiring large or uniquely shaped components, sand casting remains a trusted technique. This traditional method uses sand moulds to create parts of all sizes and complexities. It’s highly adaptable, making it ideal for custom jobs or parts that don’t fit standard moulds.
Despite its long history, sand casting has evolved with modern technology. Today’s techniques ensure better surface finishes and tighter tolerances than ever before. Industries like energy and construction frequently turn to sand casting for its affordability and flexibility, proving that this method is far from outdated.
Tackling Casting Challenges with Porosity Sealing
Even with the best processes, imperfections like porosity can occasionally occur in cast metal parts. Porosity, or tiny air pockets trapped within the metal, can weaken components and lead to issues down the line. That’s where casting porosity sealing and impregnation come into play.
Through advanced sealing techniques, these imperfections are addressed, improving the integrity and longevity of cast parts. Impregnation involves filling the pores with a sealing material, ensuring that parts are leak-proof and strong enough to withstand rigorous use. It’s a simple yet effective way to enhance the performance of metal components, especially for applications in demanding environments.
The Value of Professional Expertise
Navigating the world of casting methods and materials can feel overwhelming, but the right team can make it seamless. Whether it’s selecting the best casting method for your project or addressing challenges like porosity, working with a professional ensures that every detail is handled with care.
A company like Alliance Connect can guide you through the process, from design to final delivery. Their expertise ensures that you get parts tailored to your specifications, delivered on time and within budget. With their commitment to quality and innovation, you can trust that your project is in capable hands.
Elevate Your Manufacturing Game
Metal casting isn’t just about shaping metal—it’s about shaping the future of manufacturing. From lightweight, precise aluminium die-cast components to rugged, reliable sand-cast parts, the possibilities are endless. By working with experts who bring knowledge, technology, and a commitment to excellence, you can ensure that your products meet the highest standards of quality and performance.
So, whether you’re designing the next big thing or maintaining the tried-and-true, start with a strong foundation. Choose processes that deliver exceptional results and a team that makes it all possible.