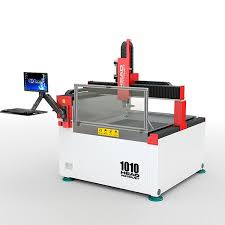
Waterjet cutting is a process in which materials are cut by high-pressure water. It has a range of applications and can cut irregular shapes from almost any material with exceptional precision and edge quality. These characteristics make it the preferred cutting method for precision, high-quality parts used in aircraft, automotive, architectural systems and more. Curves, straight cuts, internal holes and lettering, once cut by hand, can now cut in a fraction of the time.
How Does a Waterjet Work?
CNC-controlled cutting head uses a high-speed jet of water in the waterjet cutting process to cut the workpiece along a programmed path. Most materials are cut using a granular abrasive, such as garnet or aluminum oxide is added to the water stream. Water jets can be used to cut foam, food, rubber and other soft materials without using abrasives. In contrast, water jets with abrasive are required for cutting metals, stone, wood, ceramics and glass.
Most waterjet cutting machines can be easily switched between pure waterjet cutting and abrasive waterjet cutting, allowing the process to be used for almost all material types. Although waterjet cutting machines can be configured in several ways, they usually consist of the following pieces:
High-Pressure Pump
Waterjet cutters use high-pressure water pumps, which create 40,000 to 90,000 psi pressure to produce a supersonic cutting stream.
Cutting Head and Nozzle

The pressurized water flow passes through a jewel orifice with the diameter of a hair, forming a sharply defined water jet at the cutting head. When cutting with the abrasive water stream, the stream draws a predetermined amount of granular abrasive. The supersonic stream then passes through a mixing tube or waterjet nozzle where the water accelerates the abrasive. This combined flow has enough kinetic energy to cut through over a foot thick of hard materials.
Catcher Tank
After cutting the piece, the energy of the jet is absorbed in a water-filled collection tank.
Abrasive Delivery System
A pressurized abrasive hopper delivers the garnet through piping to the cutting head. The garnet is metered into the cutting head with the abrasive glow control system.
CNC Motion Control System
A high-precision motion control system precisely guides the multi-axis cutting head along a predefined cutting path. This system consists of a software program, an operator interface, a CNC control panel and servo drive motors.
What Can a Waterjet Cut?
The waterjet cutter can also be adapted for different materials. This flexibility makes it possible to cut through an incredible range of materials, including:
- Water cutting is a cold-cutting technique that allows metals to be cut without deforming them or thermally altering their properties. Carbon steel, aluminum and titanium are often waterjet cut to produce high-quality, high-precision components used in critical applications.
- While superalloys are challenging to cut using traditional methods, waterjet cutting allows them to be cut quickly and accurately. Superalloy parts which has been waterjet cut are used in everything from jet and rocket engines to submarines and nuclear reactors.
- Water jets can be used to cut plastics of different densities and thicknesses, making it possible to produce high-quality plastics used in medical devices, food manufacturing equipment and more.
- Thanks to its ability to cut through glass without breaking it, waterjet cutting is ideal for making mirrors, window panels, tabletops, solar panels and other custom-shaped glass products.
- Stone, tiles, marble, granite and other materials can be efficiently and accurately cut to different shapes with the waterjet. Waterjets are typically used to carve decorative inlays and medallions.
- Waterjet cutting is ideal for difficult-to-cut ceramic materials, making it the preferred cutting option for electrically insulated ceramic parts used in aerospace.
- Waterjet cutting can produce the intricate shape and profiles required to form of custom foam cases, dividers, insert materials, padding and other products. Waterjets cut foam without using an abrasive.
Benefits of Waterjet Cutting
Some of the advantages that distinguish waterjet cutting from other cutting techniques are:
Cost-Effectiveness
Compared to other precision cutting methods, the operating costs of a waterjet cutter is highly competitive. Additional cost- and time-saving benefits are realized through fast drawing-to-cutting transition times, quick setup and rapid cutting speeds – enabling reduced times for carrying out the work.
Superior Edge Quality
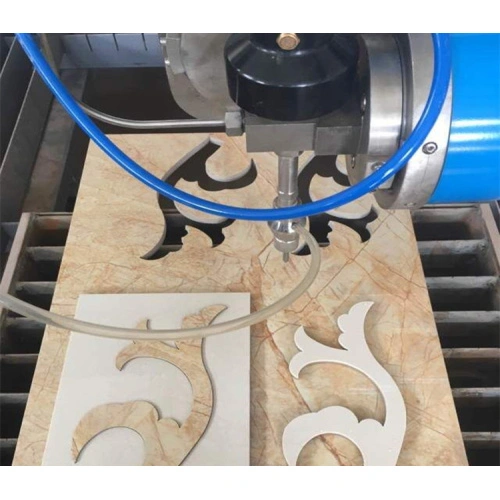
Smooth cuts created by waterjet are kept to a minimum burr, saving time and money by reducing or eliminating the need for post finishing.
Exceptional Accuracy
Waterjet cutting can achieve tolerances as close as +/- 0.002” (+/- 0.05mm), which depends on the system. This capability makes it the preferred choice for high-precision parts requiring complex design and tight tolerances. Where higher accuracy is needed, waterjets are a natural fit for finish machining processes because a waterjet cut has pristine, unhardened cut faces.
Green Benefits
Waterjet cutting is an inherently environmentally friendly process that eliminates the slag, toxic fumes and smoke common with thermal cutting methods such as plasma or laser cutting. Also, no chemicals or lubricants are used in waterjet cutting. In addition, most of the waste is shredded garnet – an environmentally benign by-product.
Interested in waterjet cutting? Check out Vehglass in Melbourne, Victoria. Their 25 years of industry experience makes their work unparalleled.